モノを造るヒトの想い|【Tras】新田正直さん「自分の造ったバイクで世界一を獲る!」
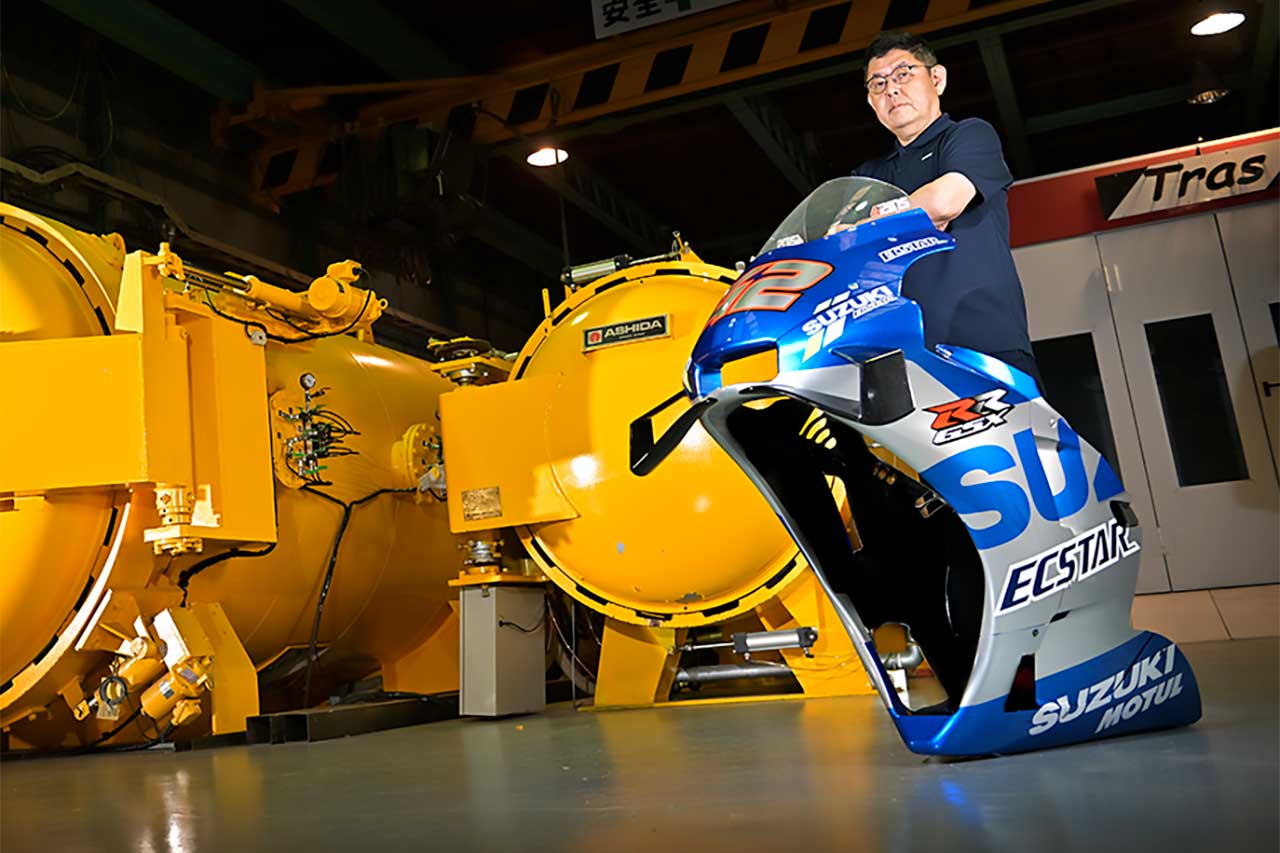
MotoGPの技術面で、今最も注目されているのが空力。スズキGSX-RRの外装を手がけたのが、カーボンパーツ専業メーカーのTrasだ。同社の創業者であり、今も第一線のカーボン職人として活躍する新田正直さん。世界トップレベルの技術力を、如何にして身につけたのかを聞く。
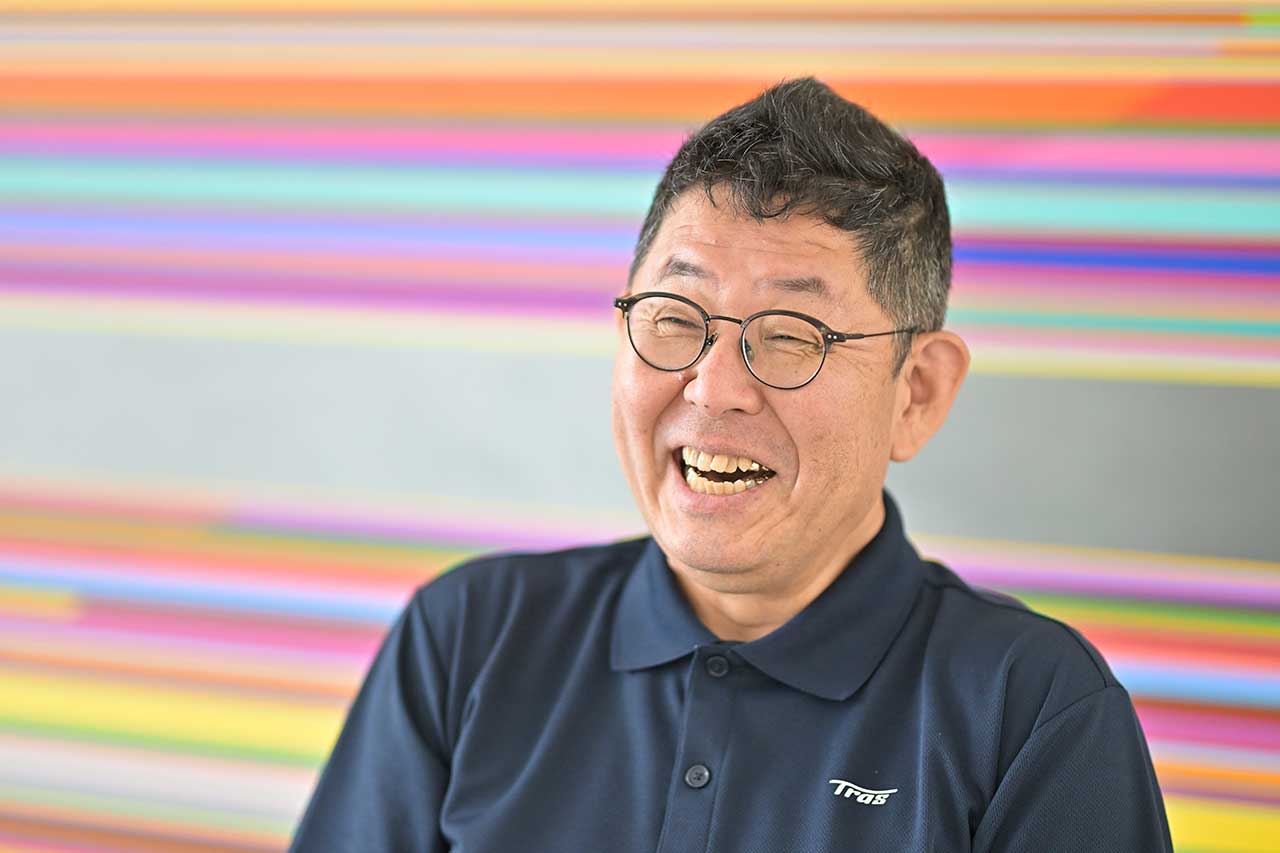
PHOTO/A.SEKINO, K.ASAKURA, S.MAYUMI TEXT/K.ASAKURA 取材協力/トラス TEL055-977-9922 https://www.tras.co.jp/
半世紀の時を経て実現した夢、自分の造ったバイクで世界一を獲る!
今回ご登場いただくのは、トラス代表の新田正直さん。そう聞いて、ピンとくるのはよほどのレースマニアだろう。
トラスは、スズキのMotoGPマシンGSX-RRをはじめ、二輪、四輪を問わずワークスマシンのパーツや試作を手がける、いわゆるBtoBのカーボンパーツメーカーだからだ。一般ユーザーからは縁遠いかもしれないが、業界ではビッグネーム。
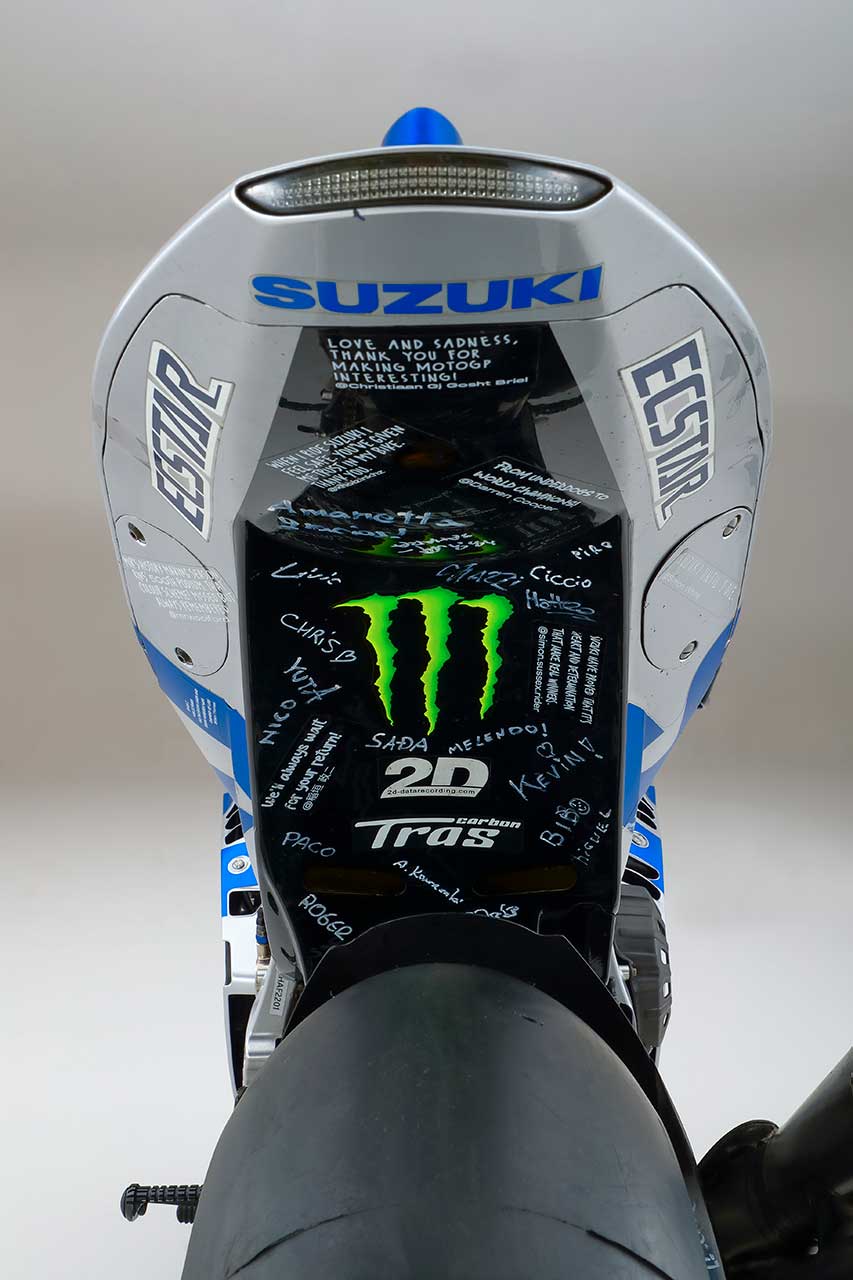
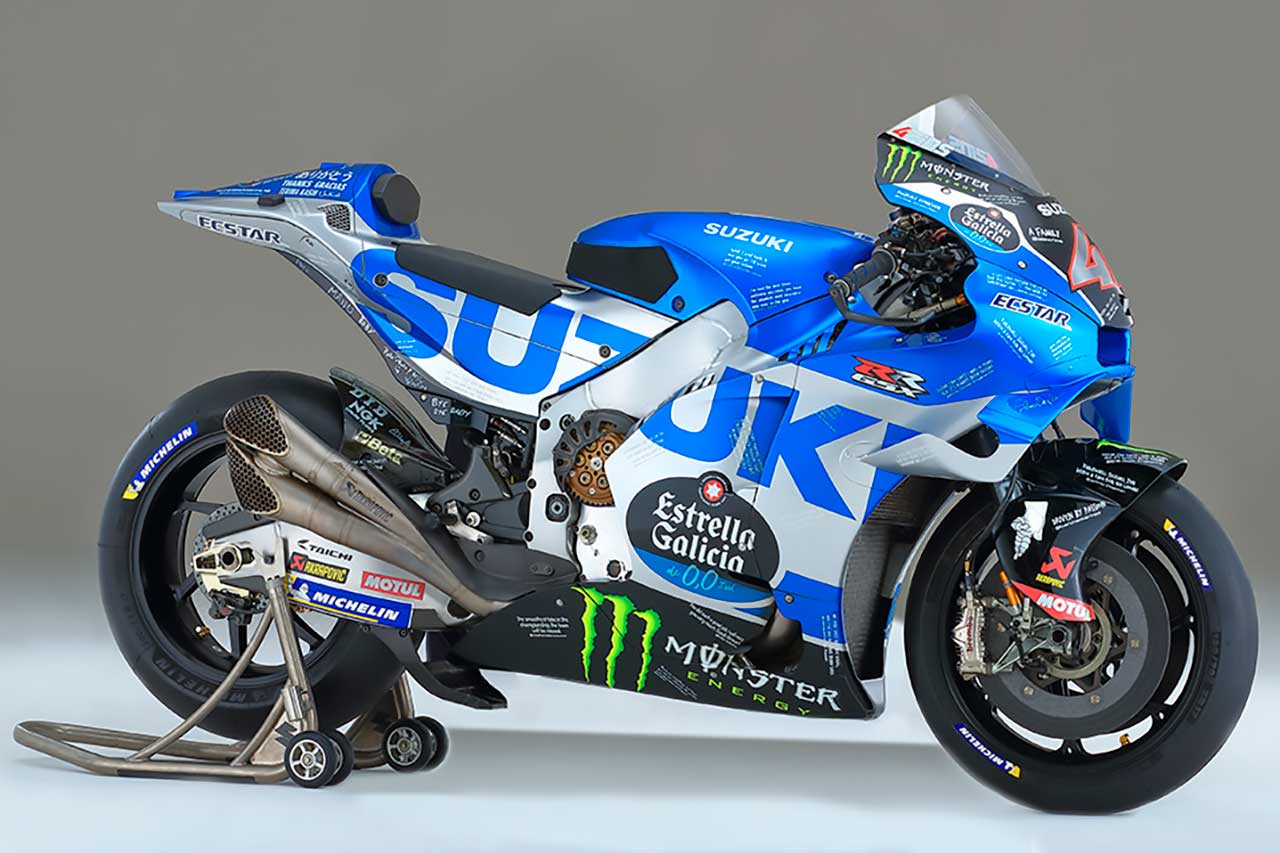
新田さん自身、日本有数のカーボン職人だその新田さんが生を受けたのは、静岡県の熱海。生まれた時から、常にバイクが身近にある環境だった。
「親父がバイク屋をやっていたんです。カワサキの販売店でした。モトクロスのチームを運営していたので、店にはいつもチーム員がたむろしていましたね。夜になったら、我が家で晩メシを食う……みたいな」
新田さんが物心ついた時には、競技からは引退していたが、お父さんは速いライダーであったようだ。
「後々調べたら、第3回浅間火山レースのリザルトに名前が残っていましたね。高橋国光さん(1960年代に世界GPで活躍、後に四輪レースに転身)と同じクラスを走っていたみたいです。親父はリタイアしていましたけど(笑)」
そんな環境で育った新田さん、当然のこととしてレーシングライダーを志すようになる。
「小学校低学年の頃にミニトレ(ヤマハGT50 大ヒットした原付トレールバイクの先駆け)が発売になってね。一生懸命お金を貯めて、小学5年生の時に手に入れました。バイク雑誌の売買欄で見つけて、モトクロスチームのメンバーが引き上げてきてくれました。3万5000円でしたね。もう夢中で、近所の山の中を走り回っていました。子供がバイクに乗っているのに、おまわりさんからも『気をつけなよ』と言われる程度。のどかな時代でした」
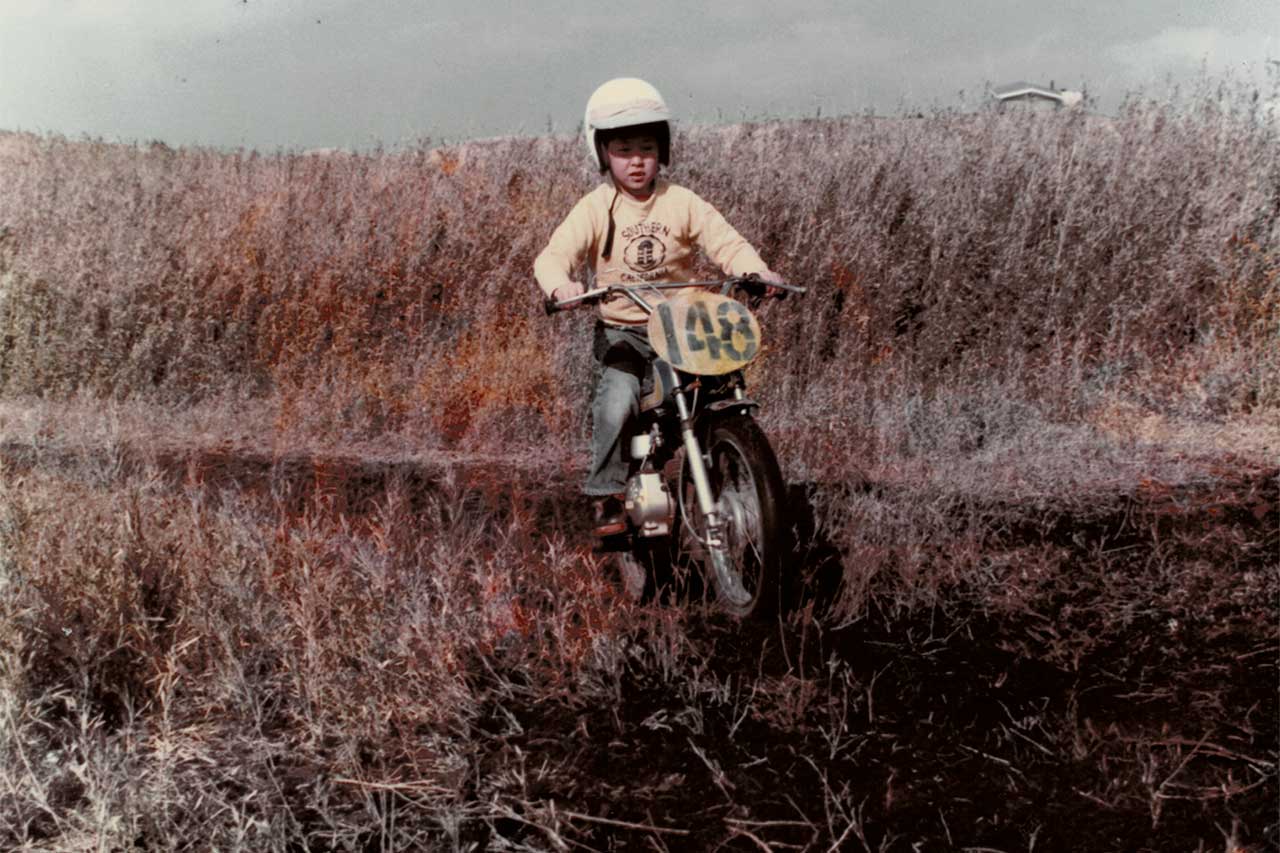
だが、レーシングライダーの道は早々に諦めることになってしまう。理由は身体的な問題だった。
「小さい頃は、ヒドい喘息持ちだったんです。それこそ、月の半分は寝込んで学校を休んでいるような子供でした。運動なんかもっての外ですから、とにかく体力が無かったんです。バイクで走っていても、すぐに息が切れるし、無理をすれば発作が出る。『自分にライダーは無理だ』と、すぐに思いしらされましたね」
少年時代の挫折。どれほど心に暗い影を落としたことだろう。
「そうでもなくて『やっぱダメか?』くらいの軽いノリでしたよ(笑)」
生まれた時から病に悩まされたことで、諦観した子供であったのかもしれない。だが、それ以上に強い意志とバイタリティーがあった。
「バイクやクルマが好きでしたし、造り手として頑張ればいいと考えたんです。自分の造ったバイクやクルマで世界一になれば、それも掛け値なしに世界一だろうって」 高校を出ると、FRPの会社に就職。もっとも、バイクやクルマのパーツとは全く関係ない、工業関係の機械カバーを造っていた。「それでも、ことあるごとに『バイクやクルマに関わりたい』と言っていたら、四輪のエアロパーツを造らないかと声をかけてもらえたんです」
トラスが工場を構える三島市は、富士スピードウェイが近い。需要は少なからずあった。22歳で独立、それから数年が経ち転機が訪れる。ドライカーボンと出会ったのだ。
「最初はトヨタのCカー(クローズドボディのレースカー)のパーツでした。ただ、その頃はカーボンの扱い方なんて誰も知らない。まともに成形できなくて、図面通りの形にするためにパテを盛りまくったりしましたね。当然、製品としてはダメ。カーボンの素材も出回っていなくて、発注元からの支給品でした。失敗はできないし、なによりしっかりとした製品に仕上げなければ、次の仕事はない。必死でしたね」

カーボンという未知の素材と格闘する日々、さらに大口のクライアントがレースから撤退し、受注量が大きく減るという苦難も重なった。時はバブル経済末期、四輪のエアロチューニングが流行し、周りのFRPメーカーもバブルに踊っていたが、新田さんはそんな世の中に背を向け、一人カーボンと向き合っていた。
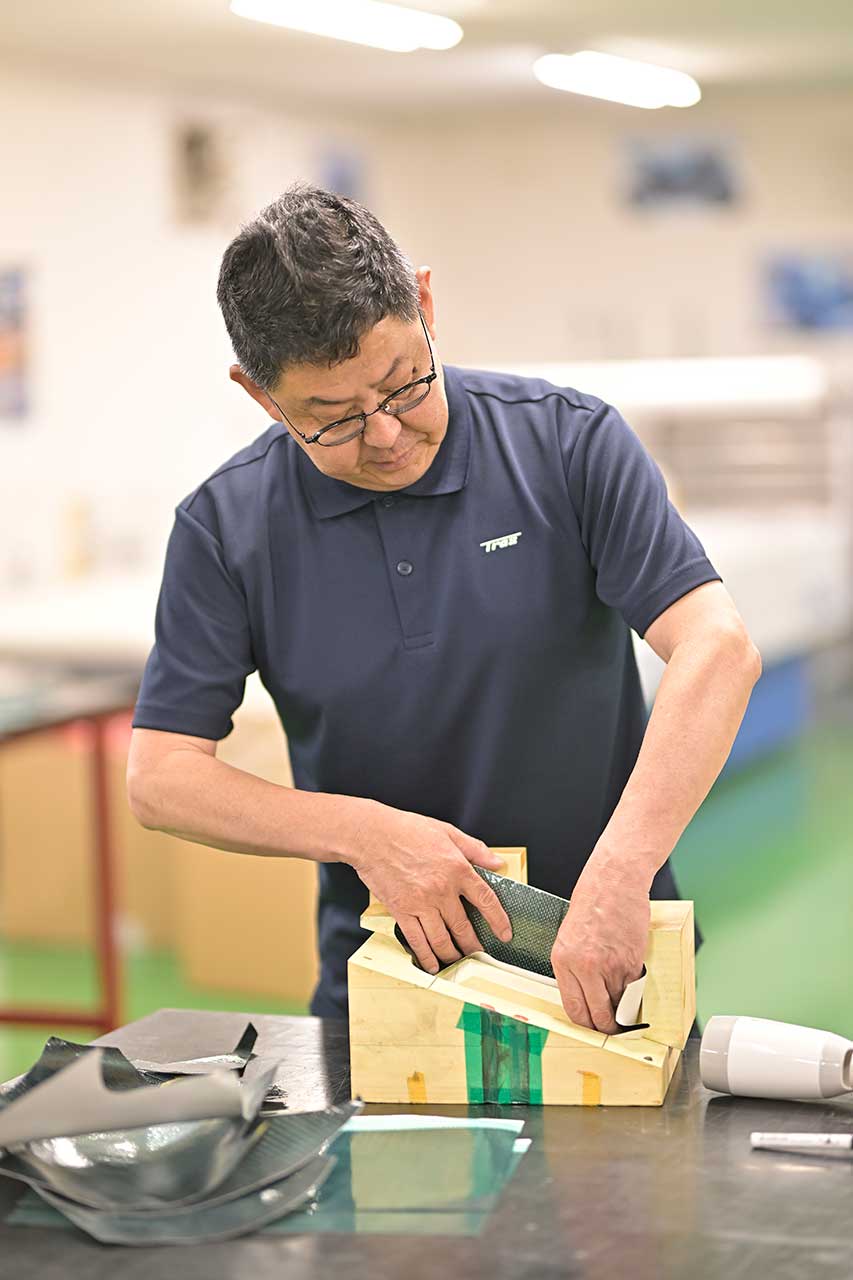
ドライカーボンのパーツは、カーボン繊維で織った布に、樹脂を染み込ませたプリプレグという素材を型に貼り込み、熱を加えて成形する。加熱時に、圧力を加えるオートクレーブという装置を使用するのが一般的だが、当時はそのオートクレーブが国内には存在しなかった。
「最初はオーブンで加熱していました。専用品などありませんから、ジェットヒーターを熱源にして、石膏ボードで囲んで断熱した手造りオーブンです。試行錯誤を繰り返して、そこそこのクオリティの製品は造れるようにはなった。ですが納得がいくものとはいえず、やはりオートクレーブが必要だと考えました」
だが、オートクレーブの導入コストは非常に高く、当時のトラスにとっては手の届かないものだった。けれど、そこで諦めないのが新田さん。国内の機械メーカーと協力し、オートクレーブの開発に着手したのだ。ここで製造装置の開発に関わったことで、カーボンという素材をより深く識ることになる。
「熱や圧力のかけかたといった、実用的なデータが得られましたし、カーボンという素材が、どのように手を加えれば、どういった形になるのか、そのメカニズムの全てが理解できたことが大きかったですね」
そうして得たノウハウがアドバンテージを産み、トラスの技術力の高さが知られるようになる。やがて、WGPマシン用パーツ製作の依頼が入り始めた。2000年代に入ると、スズキのMotoGPやSBKのマシン用パーツを手がけるようになる。
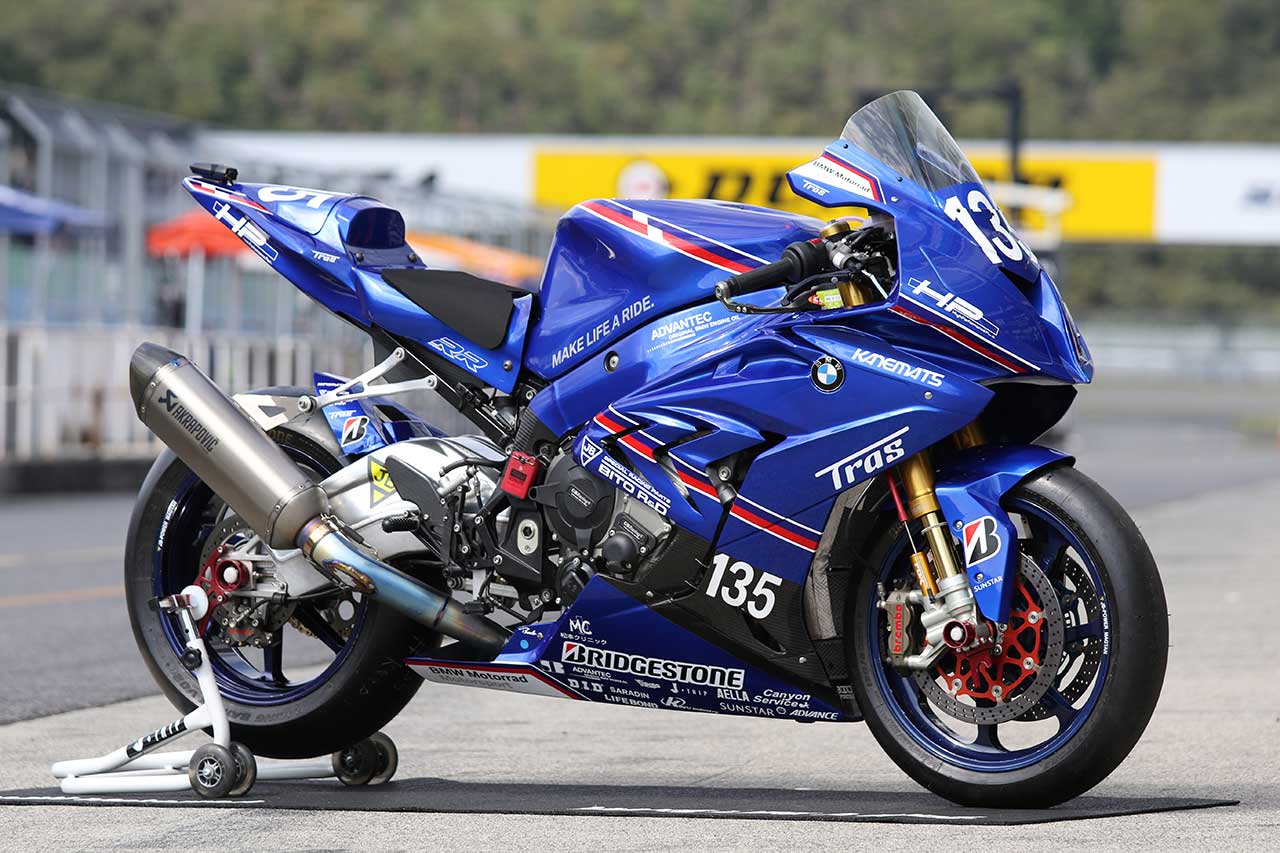
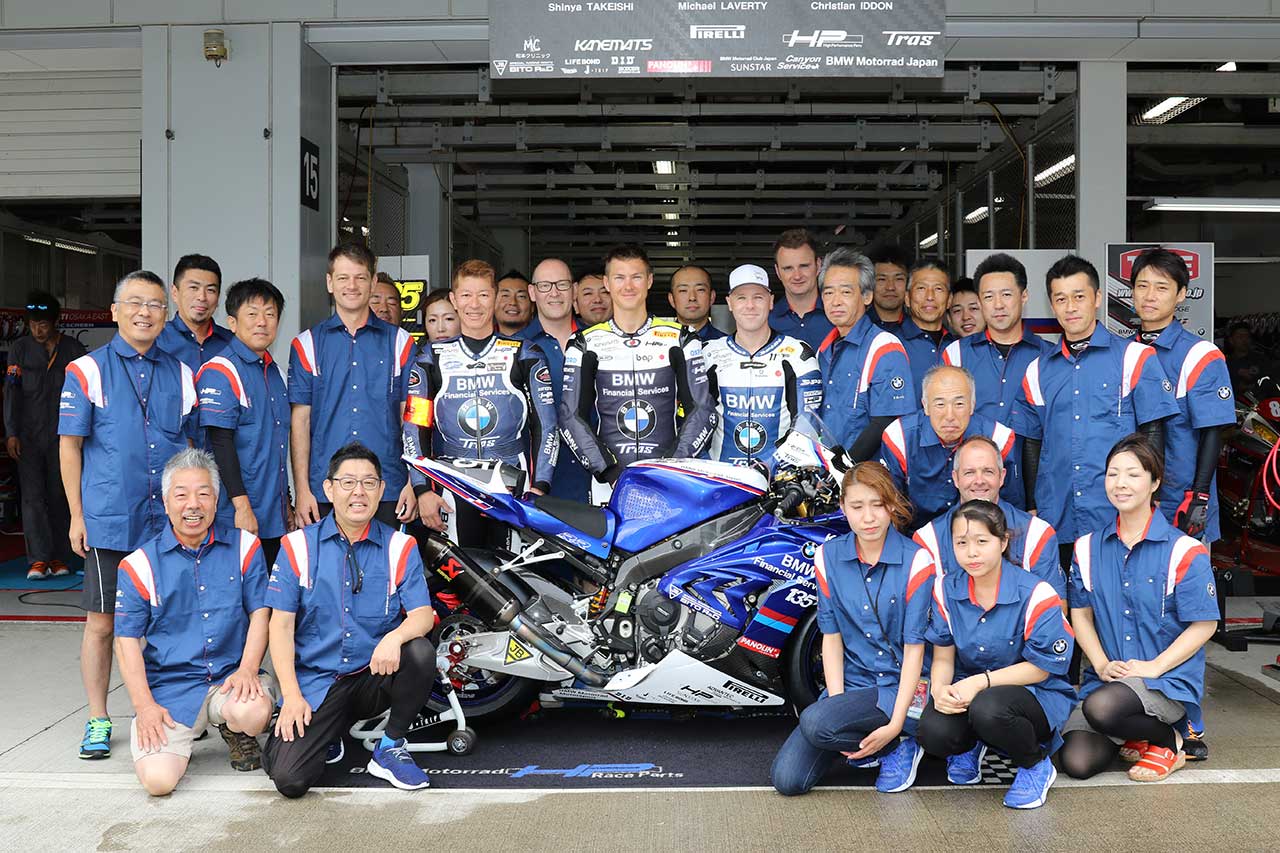
「外装パーツは、メーカーの図面通りに製作することが普通です。ですが、スズキは違いました。設計段階から参加させてもらえたので、こちらからも『こんな形も造れる』とか『こうした構造なら強度が出せる』とか様々な提案ができたんです」
近年のMotoGPは、熾烈な空力競争が繰り広げられているが、トラスはその最前線で戦った。特にウイングレットの開発は印象深い出来事だ。未開であった分野だけに進化のスピードは凄まじく、レース毎にニューパーツが投入されるような状況。トラスの工場はフル回転だった。
「スズキの設計者には『どんな設計をしてもいいから、理想の形状を追求して欲しい。絶対にちゃんとした製品に仕上げるから』と伝えていました。やりがいがありましたね」
そして2020年、トラスがカウルを手がけたスズキのMotoGPマシンGSX-RRが、チャンピオンを獲得。新田さんは、世界一のバイクを造るという、少年時代の夢を叶えたのだ。だが2022年、スズキのMotoGP撤退のニュースが届く。
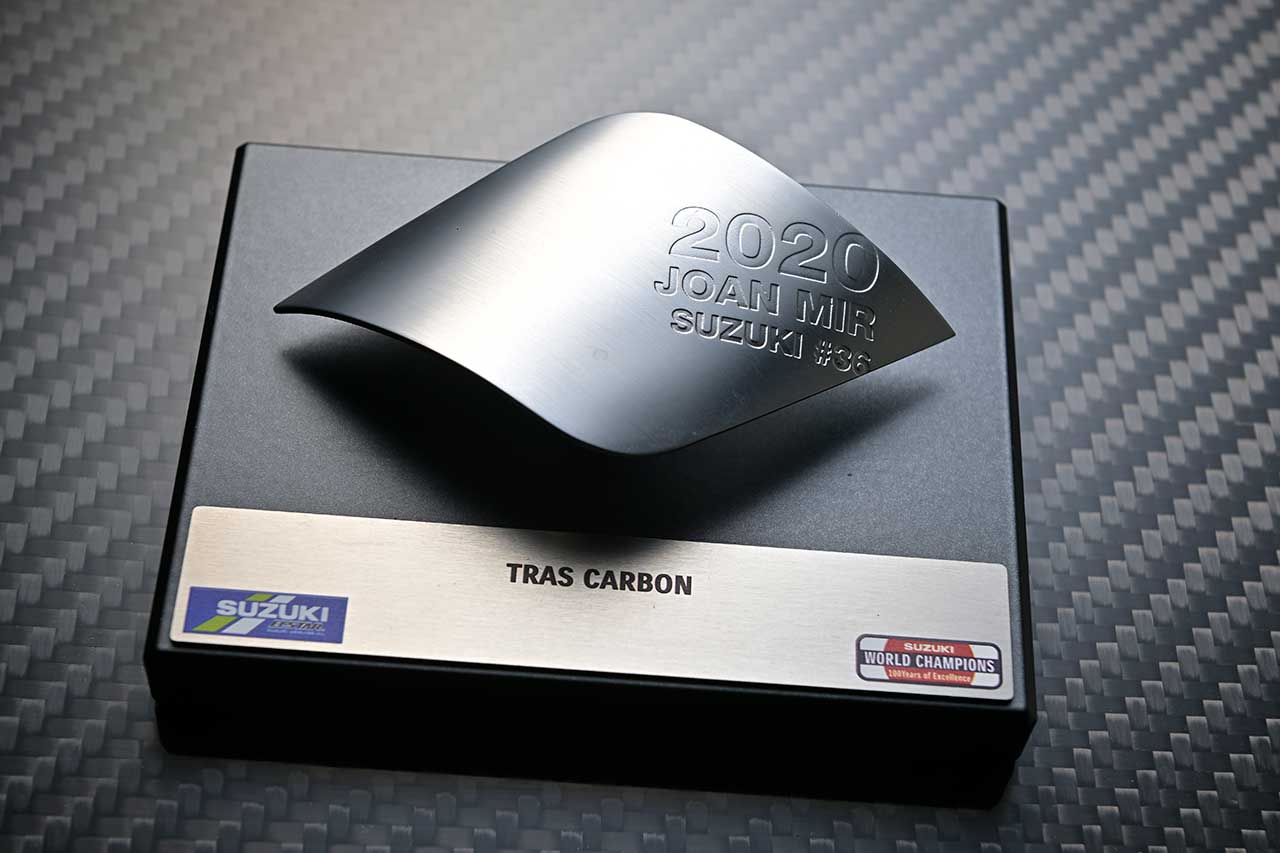
「寝耳に水でしたね。5月の連休前まで、次に造るパーツの打ち合わせをしていましたから。ビジネスの面でも痛手ですが、やはり寂しさが強かったです。スズキとの仕事は、本当に素晴らしい経験でしたから……。世界一を獲れたことで、やりきった感もあったし、もう身を引くべきか? と、考えたこともありました」
だが、新田さんは今もカーボン職人として現場に立ち続けている。トラスの技術力を見込んでの、新たなオファーがあったのだ。その内容については、残念ながらここで明かすことはできない。だが、世界トップカテゴリーのレースに関わるものであることは確かだ。
「ありがたいことに、これまで培ってきたノウハウを活かせるオファーをいただけた。自分の技術が求められているという実感が持てました。まだまだ頑張ってみよう。今は、そう思えています」
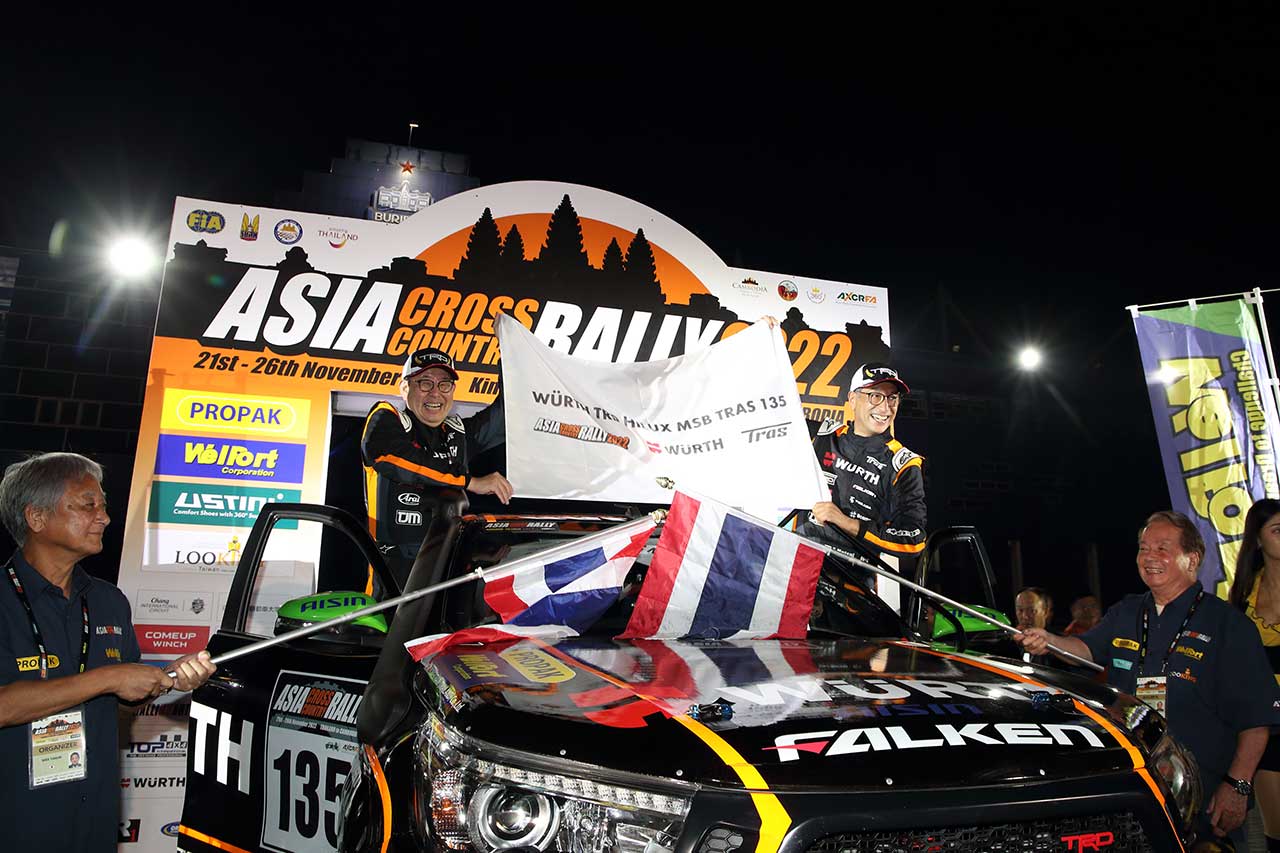
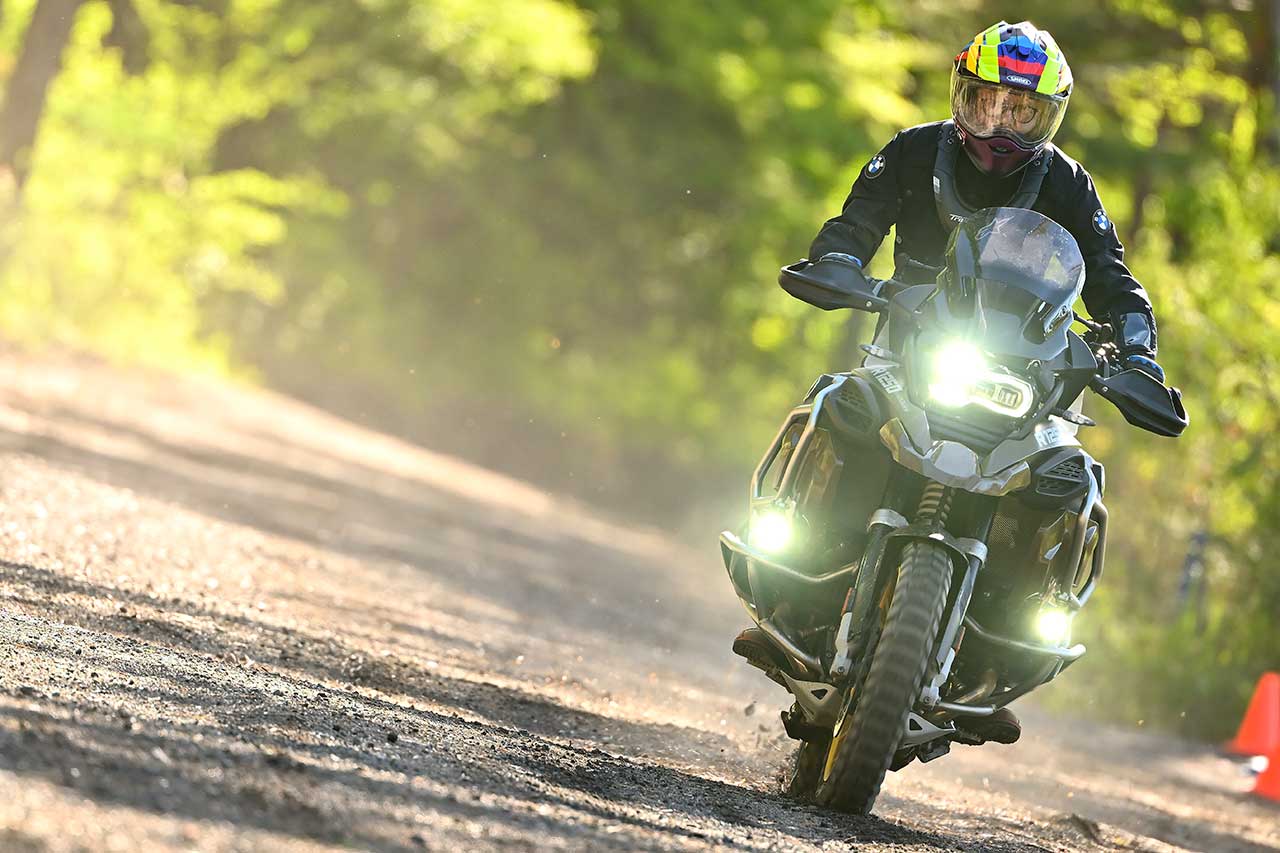